- Share
COVID-19 and Supply Chains: A Year of Evolving Disruption
From product shortages to capacity constraints in the freight sector, the coronavirus pandemic has impacted supply chains continuously if inconsistently. As COVID-19 continues to disrupt the global economy, will supply chain disruptions continue, too?
The views authors express in District Data Briefs are theirs and not necessarily those of the Federal Reserve Bank of Cleveland or the Board of Governors of the Federal Reserve System. The series editor is Harrison Markel.
the coronavirus was via disrupted supply chains because of factory shutdowns in Wuhan, China. The Federal Reserve Bank of Cleveland has monitored these disruptions for more than a year. Here, I chronicle the evolution of supply chain impacts since the beginning of the pandemic.
Start of the pandemic: Chinese factory shutdowns create ripples and uncertainty
In February and early March 2020, most business contacts we spoke with indicated that they expected the impact of factory shutdowns in Wuhan, China, to be manageable. Some noted that trade tensions in recent years had prompted many firms to diversify their supplier base. Still, given the unclear outlook, other firms said that they scrambled to find new suppliers, stockpiling items they felt might become scarce.
- February 25, 2020: A manufacturer based in Erie, Pennsylvania, reported that he anticipated there would be a bottleneck, and he said the firm was trying to diversify as quickly as it could. The firm tried to buy castings months and months ahead of its production schedule. There was a cost associated with that search, and casting prices also increased.
- February 26, 2020: A retailer based in Columbus, Ohio, said that because of trade tensions with China during the last couple of years, the firm moved a lot of its supply chain out of China; so the virus had been less of a disruption to its supply chain than it would have been in the past. However, the goods it orders from China are goods for which there are no good substitutes.
Spring 2020: Lockdowns in the United States and Europe added to product shortages
As the virus spread and governments around the world imposed stay-at-home orders, reports of supply chain disruptions increased. By April, many firms, especially manufacturers, reported that factory shutdowns led to shortages of products. These shortages persisted even though several contacts said that production came back online in China more quickly than they had anticipated. Firms were forced to search for new suppliers and, in some cases, to shuffle production schedules based on available materials and components. For firms in the region the Cleveland Fed serves, the complete shutdown of automotive assembly plants was particularly painful; suppliers were left with cancelled orders for several weeks and, correspondingly, production was shut down. Grocers and restaurateurs also noted that even as the initial surge in consumer pantry-stocking behavior subsided, COVID-19 outbreaks at meat packing facilities led to shortages and price increases into the month of May.
- April 16, 2020: A manufacturer based in Toledo, Ohio, said his firm was calling its suppliers daily so that the firm could stay on top of what was coming in order to plan production accordingly. The firm also tried to ensure it had more than one supplier for materials—a departure from past practice.
- May 21, 2020: A grocer based in Wheeling, West Virginia, reported that early in the pandemic, it was difficult to secure cleaning and paper products, but these disruptions had subsided more recently. However, with many meat processing plants shut down because of COVID-19 outbreaks among employees, it had become increasingly difficult and expensive to obtain pork and beef products.
Summer 2020: Following the reopening of economies, disruptions became idiosyncratic
During four surveys, we asked contacts whether they saw significant supply chain disruptions that hampered their operations. In each survey, around one-third of respondents indicated that they had. These results are largely consistent with responses to the US Census Bureau’s Small Business Pulse survey (see Figure 1). In that survey, the share of Ohio respondents reporting supply chain disruptions peaked in April and May and then leveled off in the early summer. In surveys throughout the rest of the year, roughly 30 percent to 35 percent of respondents reported domestic supplier delays.
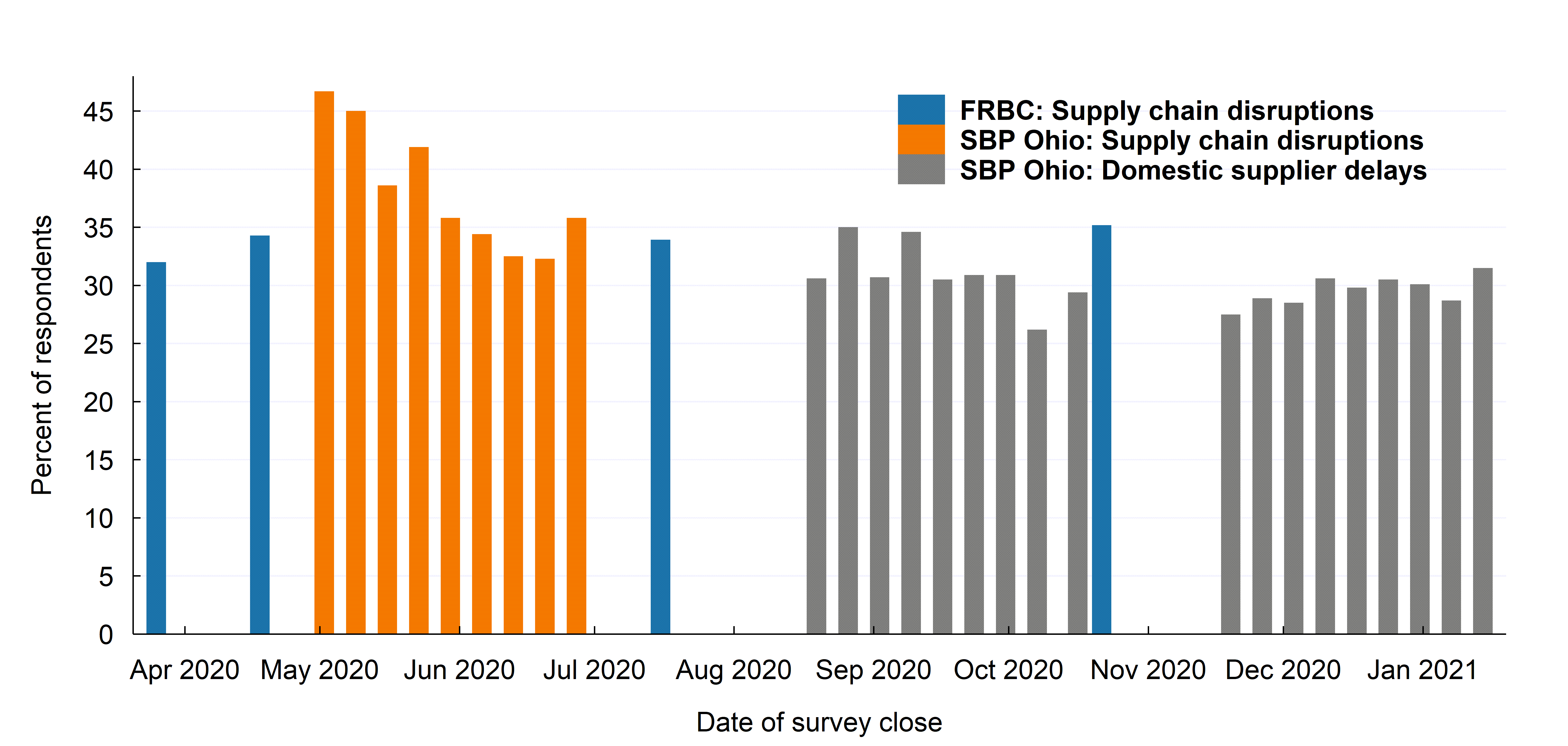
Sources: Federal Reserve Bank of Cleveland (FRBC) and the US Census Bureau Small Business Pulse (SBP) Survey.
As time passed, the nature of the disruptions and the contacts that experienced them evolved. Of the 136 contacts who responded to more than one of the Federal Reserve Bank of Cleveland’s surveys, 43 percent gave different answers at different points in time. For example, some respondents reported that supply chain disruptions hampered operations in March and April, subsided in July, but re-emerged in October.
Percent of sector that responded “Yes” | ||||
---|---|---|---|---|
March 23–30 (125) |
April 17–20 (105) |
July 13–20 (112) |
October 19–26 (108) |
|
Full sample | 32.0 | 34.3 | 33.9 | 35.2 |
Retail | 64.7 | 61.5 | 58.8 | 63.2 |
Transportation | 50.0 | 25.0 | 44.4 | 50.0 |
Construction and real estate | 44.0 | 57.9 | 42.9 | 66.7 |
Manufacturing | 25.0 | 31.0 | 27.6 | 32.1 |
Other | 11.6 | 16.7 | 23.3 | 5.4 |
Note: Total number of responses shown in parentheses.
When factories reopened and many governments lifted stay-at-home orders, reported supply chain disruptions became more idiosyncratic than they were in March and April. This was in part because the speed with which producers could reopen varied. Shuttered steel mills and automotive production lines took weeks to come back online. The automotive supply chain was further stressed because of government restrictions and COVID-19 outbreaks at factories in Mexico, contributing to low inventories for auto dealers as demand for light vehicles exceeded industry participants’ expectations. Although many contacts reported that it became easier to obtain materials and component parts in the summer than in the spring, prices for some products increased substantially. Notably, a hot housing market and an increase in do-it-yourself remodeling projects created shortages of treated lumber.
European supply chains improved somewhat during the summer months; just 8 percent of firms reporting supply chain disruptions indicated that Europe was a pain point in a survey in mid-July, down from a high of 28 percent in a survey during the last week of March (see Figure 2). However, as cases of COVID-19 began to rise and the outlook for Europe’s economic recovery was uncertain, the share rebounded to 18 percent in late October. The October survey also reported an increase in disrupted supply chains in Canada and Mexico. While the share held relatively steady at just above 20 percent in the three earlier surveys, it jumped to 32 percent in October. Additionally, the industry composition shifted somewhat: In July, half of the contacts that reported supply chain disruptions in North America outside of the United States were manufacturers, but in October, respondents were clustered in retail (primarily auto dealers) and construction and real estate.
- June 2, 2020: A residential builder based in Northeast Ohio reported paying a premium for some materials due to COVID-19 supply disruptions. He said his firm could either pay the premium to keep construction rolling or halt operations until the local supply chain rebuilt capacity.
- October 13, 2020: A manufacturer based in Cleveland, Ohio, said there had been a lot of disruption in the supply chain, with lead times from European suppliers increasing threefold from prepandemic levels. Lengthened lead times and uncertainty regarding Europe’s recovery necessitate stockpiling of materials and component parts, and “if you don’t have a large warehouse right now, you’re out of luck.”
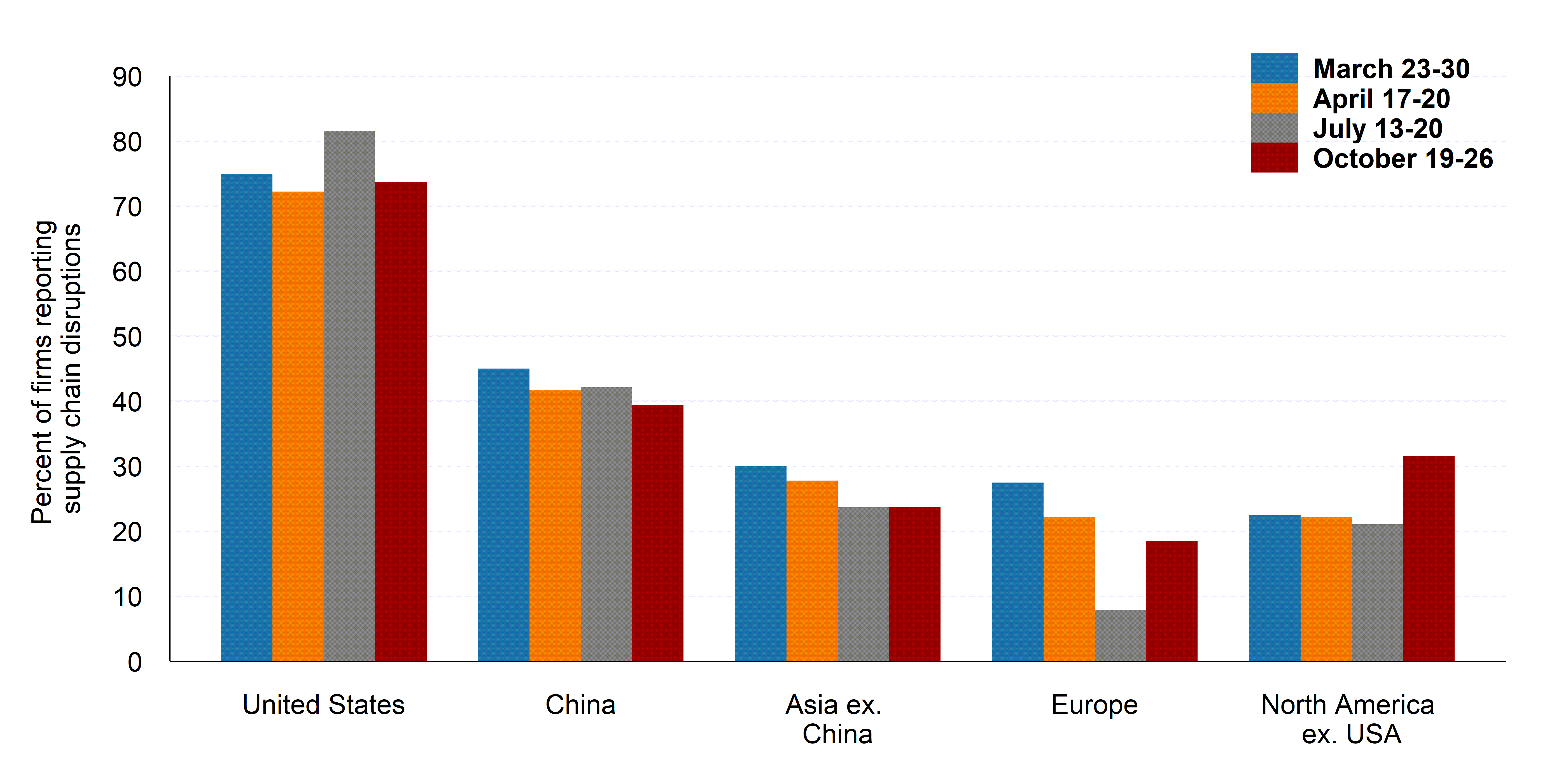
Source: Federal Reserve Bank of Cleveland
Fall 2020: Constraints in logistics networks created additional pain points
In the fourth quarter of 2020, an increase in disruptions to logistics networks piled on to the ongoing erratic parts shortages and shipping delays. Freight haulers said that in addition to a massive shift in holiday shopping from brick-and-mortar stores to ecommerce (one logistics software firm reported a record 3 billion packages were shipped during peak season), manufacturers that had kept inventories relatively lean throughout the year now found the need to replenish to keep up with stronger-than-expected demand. Meanwhile, a shortage of truck drivers was exacerbated by absences as employees contracted COVID-19 or needed to quarantine. Additionally, there was a smattering of reports that trucks were idled because repair parts were in short supply.
Strong demand for shipping combined with capacity constraints resulted in dramatic increases in freight costs and lead times. In our late October survey, 44 percent of contacts indicated that they had experienced delays in receiving products, and 16 percent reported that the base cost of shipping final goods had increased. In subsequent conversations, an increasing number of contacts reported very long lead times and steeply rising freight costs. Moreover, the surge in COVID-19 cases in the United States impacted labor availability; contacts reported that more and more products were out of stock because worker quarantines led to unmet production schedules.
- November 10, 2020: A West Virginia-based manufacturer said that the main constraint on production was staffing, not shortages of materials. Based on its past-due inventory, the firm’s production volume would be 3 percent higher if it was fully staffed. Transport lanes of all types were congested, and it took longer to receive materials. As a result, freight prices increased substantially—10 percent to 15 percent from a year ago, depending on the shipping lane.
- November 12, 2020: A freight hauler based in northern Kentucky reported that two of its biggest ecommerce customers were doing 10 times their normal volume of business. The firm had some delays receiving truck parts. Before the pandemic, it would take two to three days to receive parts. Now, it took two to three weeks. In a couple of cases, it took two months to receive shipments. The firm swapped parts out of idled trucks until it received the necessary parts.
Winter 2020-21: Logistics bottlenecks and product shortages continue
As the winter wore on, firms continued to report shortages and shipping delays. Manufacturers reported steel shortages, which ratcheted up prices (see Figure 3) as producers clamored to bring additional steel mills back online. Making matters worse, a microchip shortage threatened first quarter automotive production. Freight haulers expected demand to remain strong at least through the first quarter of 2021, and bottlenecks at ports worsened because of COVID-19 outbreaks.
- January 22, 2021: A manufacturer based in Cleveland, Ohio, said that supply chain issues continue, and they were making things scarcer (which led to delays) and more expensive. Most firms were working around the situation as best they could. Freight rates were up by more than 50 percent, and there were significant delays with the US Postal Service in particular.
- January 26, 2021: A manufacturer based in Toledo, Ohio, said that his “biggest headache” related to logistics. There appeared to be a fair amount of port congestion, which was most acute at the port of Los Angeles. They tried to move some shipments through Vancouver, and, in some cases, through the Panama Canal to ports on the east coast, but it was not much faster, and it was much more expensive.
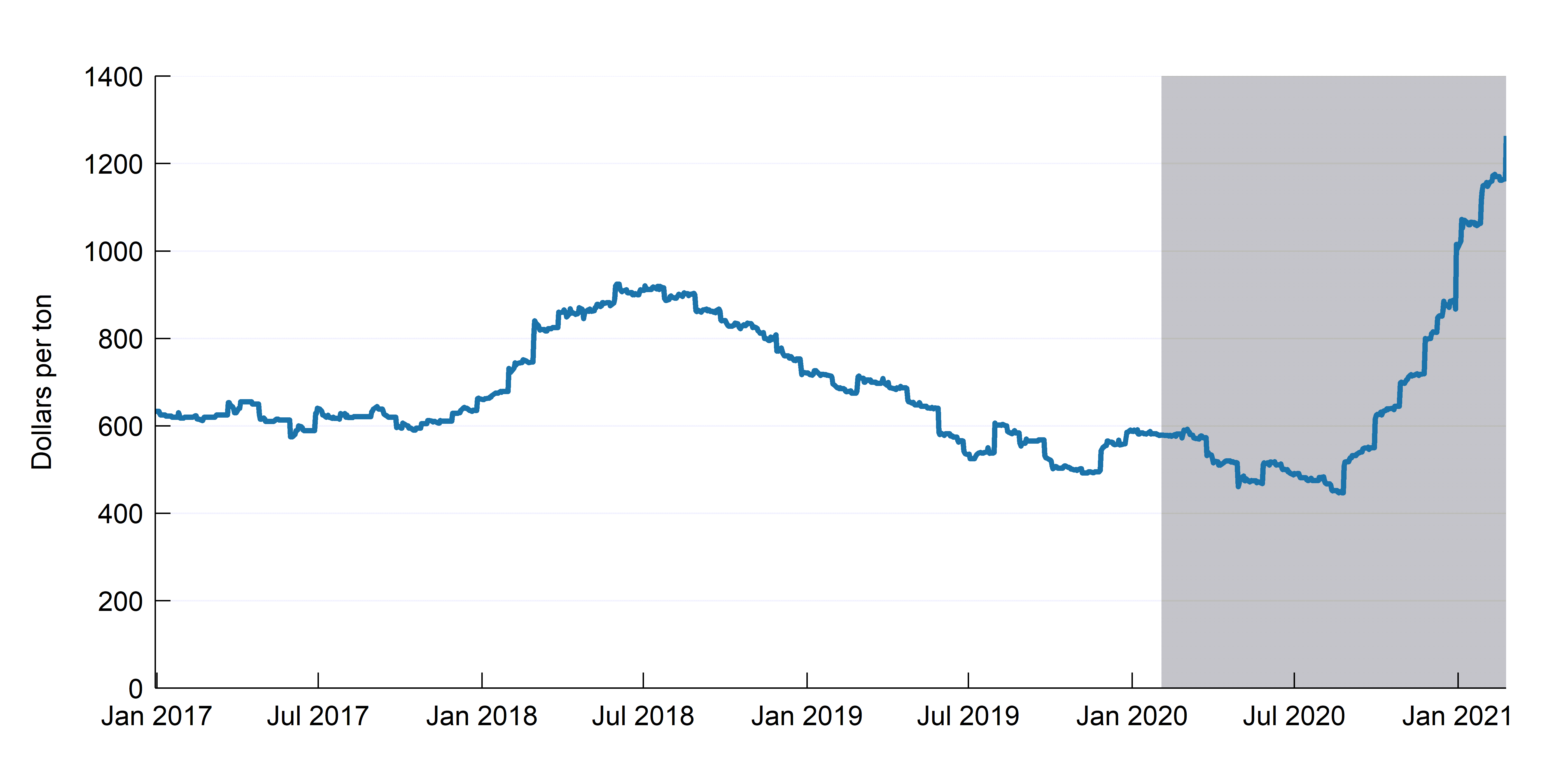
Notes: Settlement price for first expiring contract. Shading indicates recession period. Last data point is February 24, 2021.
Source: Commodity Exchange, Inc. via Haver Analytics
Conclusion: Supply chain disruptions to continue for some time
From product shortages to capacity constraints in the freight sector, the coronavirus pandemic has impacted supply chains continuously if inconsistently. As COVID-19 continues to stymie the global economy, some firms have indicated that they are hesitant to invest in additional capacity (which could ease some of the supply chain tensions) because they are unsure how long robust demand will continue. Because of this hesitancy and because the path of the virus remains unclear, it is likely that supply chain disruptions will continue to evolve for the foreseeable future.
References
- Andersen, Katy. 2020. “Coronavirus: Nationwide Lumber Shortage Affecting Local Businesses.” WHIO (July 23). whio.com/news/coronavirus-nationwide-lumber-shortage-affecting-local-businesses/MASKIRMIBFAJ5BE6QFSU7LIW7E/.
- Beresford, Colin. 2020. “Details of Increasing Plant Shutdowns amid COVID-10 Pandemic.” Car and Driver (March 25). caranddriver.com/news/a31753194/ford-gm-honda-shutdown-us-plants/.
- Boudette, Neal E. 2020. “Autoworkers Are Returning as Carmakers Gradually Crank Up Factories.” New York Times (May 17). nytimes.com/2020/05/17/business/coronavirus-auto-manufacturing-restart.html.
- Colias, Mike, and Ben Foldy. 2020. “GM’s Plans to Increase Truck Production Delayed by Parts Shortage.” The Wall Street Journal (May 22). wsj.com/articles/gms-plans-to-increase-truck-production-delayed-by-parts-shortage-11590155233.
- Esposito, Anthony. 2020. “Ford Says Restrictions at Mexico Plants ‘Not Sustainable.’” Reuters (July 9). reuters.com/article/us-usa-mexico-ford/ford-says-restrictions-at-mexico-plants-not-sustainable-idUSKBN24A38V.
- Fitzgerald, Michael. 2020. “US Auto Manufacturers and Others Facing Steel Shortage.” S&P Global Platts (November 20). spglobal.com/platts/en/market-insights/latest-news/metals/112020-us-auto-manufacturers-and-others-facing-steel-shortage.
- Greimel, Hans, and Yang Jian. 2021. “Global Microchip Shortage Hits Toyota, Honda, Nissan, German Automakers.” Automotive News (January 8). autonews.com/automakers-suppliers/global-microchip-shortage-hits-toyota-honda-nissan-german-automakers.
- Jindel, Satish. 2021. “With Over 3 Billion Parcels Delivered in Peak, Expect a New Record for Returns.” ShipMatrix (January 5). shipmatrix.com/wp-content/uploads/2021/01/SM_-Over-3-billion-parcels-delivered-in-peak-2020_Jan-5_2021.pdf.
- Klayman, Ben. 2020. “U.S. Auto Sales in May Encourage Detroit Plan to Rebuild Inventories.” Reuters (June 2). reuters.com/article/us-usa-autos-demand-idUSKBN2392HO.
- Pete, Joseph S. 2020. “U.S. Steel Restarts Blast Furnace #4 at Gary Works as Conditions Recover.” NWI Times (December 1). nwitimes.com/business/local/u-s-steel-restarts-blast-furnace-4-at-gary-works-as-conditions-recover/article_61b32de8-143e-5cf7-9eef-0d9a7cada5dd.html.
- Reuters Staff. 2020. “Timeline: How the Global Coronavirus Pandemic Unfolded.” Reuters (September 28). reuters.com/article/us-health-coronavirus-timeline/timeline-how-the-global-coronavirus-pandemic-unfolded-idUSKBN26K0AQ.
- Roosevelt, Margot. 2021. “Could a COVID-19 Surge Lead to Shutdowns at L.A. Ports? Officials Plead for Dockworker Vaccines.” Los Angeles Times (January 20). latimes.com/business/story/2021-01-20/covid-surge-hits-la-ports-increasing-need-for-vaccines.
Suggested Citation
Dunn, Julianne. 2021. “COVID-19 and Supply Chains: A Year of Evolving Disruption.” Federal Reserve Bank of Cleveland, Cleveland Fed District Data Brief. https://doi.org/10.26509/frbc-ddb-20210226
This work by Federal Reserve Bank of Cleveland is licensed under Creative Commons Attribution-NonCommercial 4.0 International